Why Businesses Rely on Packaging Equipment Repair Services for Equipment Longevity
Why Businesses Rely on Packaging Equipment Repair Services for Equipment Longevity
Blog Article
Recognize the Advantages of Using Specialist Product Packaging Equipment Repair Provider
Using specialist product packaging devices fixing services offers a number of essential benefits for organizations. Boosted equipment long life and boosted operational performance are notable advantages. Competent service technicians can rapidly attend to issues, preventing minor troubles from rising into considerable downtime. Additionally, routine upkeep supports conformity with industry standards, guaranteeing safety and protecting brand name credibility. Recognizing how these elements add to overall performance is vital for any organization seeking to enhance its procedures. What effects does this have for future growth?
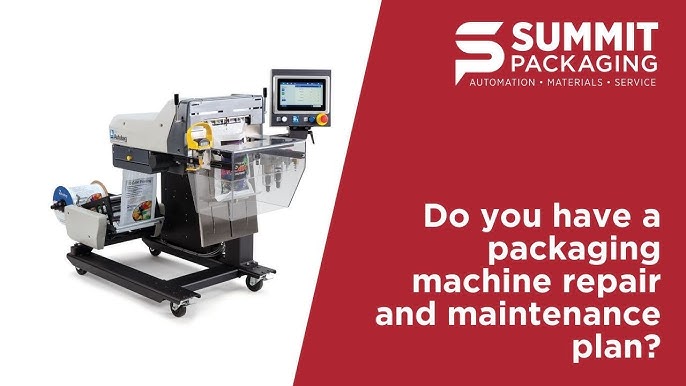
Improved Equipment Longevity
Appropriate upkeep via professional packaging devices repair service solutions considerably adds to improved tools longevity. By resolving damage quickly, these services help prevent small issues from rising right into major break downs. Skilled professionals possess the requisite understanding and proficiency to recognize prospective troubles that may not be obvious to inexperienced personnel. Regular inspections and timely repair work assure that machinery operates within optimal specifications, reducing the threat of disastrous failures.Moreover, professional fixing solutions frequently use top quality substitute components, which can considerably prolong the life-span of devices. This aggressive technique not only minimizes downtime however likewise promotes a constant manufacturing flow. Services that buy specialist maintenance are most likely to see an extra trustworthy performance from their product packaging equipment, eventually bring about lowered expenses related to constant replacements. Essentially, the longevity of packaging equipment is straight affected by the commitment to regular and experienced fixing solutions.
Enhanced Operational Efficiency
Buying expert product packaging devices repair work solutions straight improves functional efficiency (Packaging Equipment Repair Services). Specialist service technicians possess specialized knowledge and abilities, allowing them to diagnose and resolve issues promptly, decreasing downtime. By making sure that devices runs at peak performance, companies can preserve consistent manufacturing timetables, therefore satisfying client demands much more effectively.Furthermore, normal upkeep and prompt repair services stop small problems from intensifying right into considerable malfunctions, which could interrupt operations and lead to pricey delays. With properly repaired tools, employees can concentrate on their core jobs instead of troubleshooting malfunctioning machines.The dependability of well-kept product packaging devices adds to smoother procedures, making it possible for business to maximize their production procedures. Inevitably, this proactive strategy not just improves procedures however also cultivates a more productive work atmosphere, enabling companies to adapt to transforming market requires with greater agility. Enhanced functional effectiveness ends up being a keystone for sustained development and competition in the product packaging sector
Expense Savings on Services
Implementing professional product packaging tools repair solutions can lead to considerable expense savings for companies. By addressing repair needs immediately and successfully, companies can stay clear of the high costs connected with prolonged tools downtime. Delays in fixing equipment can result in lost production, which straight impacts revenue. Additionally, expert repair service services frequently supply mass or regular maintenance, lowering the chance of major break downs in the future.In addition, making use of specialized services can expand the life expectancy of devices, lessening the need for costly substitutes. Businesses can additionally take advantage of predictable repair work prices, permitting for far better budgeting and financial preparation. Contracting out repair services can release up interior sources, making it possible for team to focus on core procedures instead than fixing equipment concerns. In general, professional packaging equipment repair service services provide a critical strategy to managing repair service expenditures, inevitably boosting a business's profits while ensuring operational connection.
Access to Specialist Understanding and Abilities
While services might have competent staff, relying upon professional packaging devices fixing solutions offers access to a broader series of professional knowledge and specialized abilities. These experts are typically trained in the most up to date modern technologies and industry standards, which enables them to deal with complicated problems that in-house groups might not be furnished to deal with. Their experience spans numerous equipment kinds and brands, enabling them to quickly identify troubles and apply efficient solutions.Moreover, expert repair work professionals stay updated on innovations and finest techniques, making sure that repairs are carried out successfully and efficiently. This degree of know-how can bring about improved devices longevity and performance, inevitably profiting the firm's lower line. By using these specialized services, businesses can touch into a riches of expertise that boosts their functional capacities without the requirement for extensive inner training or investment in additional sources. This critical technique assists preserve the honesty of product packaging processes while enhancing source allowance.
Minimization of Downtime
Minimizing downtime is necessary for preserving functional efficiency in product packaging facilities. Quick feedback times, combined with specialist troubleshooting skills, allow service technicians to resolve issues quickly. Furthermore, effective repair service procedures guarantee that tools is restored to come to a head efficiency with very little disruption.
Quick Reaction Time
A speedy reaction time is necessary for companies depending on product packaging tools, as even minor hold-ups can bring about significant operational disruptions. When equipment malfunctions, punctual attention from expert repair solutions can drastically lower downtime, enabling manufacturing timetables to resume promptly. Quick response times not just reduce the influence on general productivity yet additionally assist keep consumer satisfaction by conference distribution timelines. Specialist repair work services commonly prioritize urgent requests, making certain that professionals are readily available to resolve concerns as they emerge. This degree of responsiveness is essential in competitive sectors where efficiency is paramount. Inevitably, businesses gain from a trustworthy collaboration with fixing solutions that comprehend the necessity of their functional requirements, cultivating an aggressive approach to devices upkeep and administration.
Professional Troubleshooting Abilities
Professional troubleshooting abilities are vital for reducing downtime in product packaging procedures. Knowledgeable service technicians possess the ability to promptly recognize the origin of equipment breakdowns, which is essential in preserving operational effectiveness. They use their comprehensive knowledge and experience to detect issues accurately, making sure that prospective troubles are addressed prior to they rise. This aggressive technique decreases the threat of extended blackouts and boosts efficiency. In addition, professional troubleshooters can apply targeted solutions that prevent recurring issues, causing a much more dependable product packaging process. Their proficiency not only conserves time yet also decreases the monetary effect of unexpected failures. In an industry where time is cash, having accessibility to skilled troubleshooting skills is an important possession for any type of packaging procedure.
Efficient Fixing Processes
Effective fixing processes play a crucial duty in decreasing downtime for packaging equipment. like this Fast diagnosis and reliable implementation are important elements that enable service technicians to determine issues quickly and carry out services without unnecessary delays. Expert repair services usually make use of innovative tools and technologies, allowing for even more accurate repairs and decreasing the likelihood of persisting issues. Standard treatments and structured operations improve the repair service procedure, ensuring that repair work are completed consistently and efficiently. This effectiveness not just recovers equipment functionality yet additionally boosts overall functional productivity. By spending in specialist repair service solutions, organizations can significantly decrease the moment equipment remains idle, informative post ultimately leading to boosted earnings and functional dependability in their packaging procedures.
Conformity With Sector Requirements
Conformity with market requirements is necessary for making sure the stability and safety of packaging devices. Adhering to governing demands and devices safety criteria not just safeguards employees but likewise boosts functional performance. Carrying out market ideal methods is crucial for maintaining compliance and fostering a society of security and quality within organizations.
Regulatory Conformity Guarantee
Making sure regulative conformity in packaging devices fixing is crucial for preserving industry criteria and guarding product honesty. Expert repair work services are skilled in the certain policies governing packaging procedures, ensuring that all fixings satisfy the required legal needs. This experience reduces the danger of non-compliance, which can lead to expensive penalties and interruptions in manufacturing. Furthermore, adherence to regulative standards assists in protecting brand name online reputation and customer depend on. By utilizing specialized repair service services, companies can streamline their operations while making certain that their equipment operates within the framework of market regulations. This aggressive approach not only improves operational effectiveness but also strengthens commitment to quality and safety in the product packaging field.
Devices Security Criteria
While many business focus on performance in their packaging procedures, adherence to equipment safety requirements is crucial for avoiding crashes and making certain a secure functioning setting. Compliance with these criteria aids reduce risks related to equipment usage, securing both staff members and properties. Specialist packaging devices repair solutions play an essential duty in maintaining safety by ensuring that machines are regularly examined, serviced, and updated according to industry laws. This aggressive strategy not just enhances operational dependability however also cultivates a society of safety and security within the office. By buying professional fixing services, business can achieve conformity with safety criteria, minimize responsibility dangers, and eventually promote a more secure, a lot more productive atmosphere for their labor force.
Industry Best Practices
Sticking to market finest methods is necessary for packaging business intending to keep functional quality and regulative compliance. Compliance with sector criteria not just boosts item quality yet additionally decreases risks linked with equipment breakdowns and safety dangers. Regular training and certification for specialists guarantee that they are skilled in the latest fixing methods and safety protocols. In addition, regular maintenance timetables aid in identifying possible concerns before they escalate, thus lengthening tools life. Making use of standardized procedures and documentation practices helps with uniformity and accountability. By accepting these ideal techniques, product packaging business can boost efficiency, decrease downtime, and foster a culture of security and dependability, inevitably leading to raised client contentment and loyalty.
Boosted Security in the Office
As business focus on the health and safety and security of their staff members, the role of expert product packaging tools repair solutions comes to be progressively important in boosting workplace safety. Properly maintained tools considerably reduces the threat of accidents, injuries, and tools malfunctions. Professional technicians have the knowledge to determine potential hazards and carry out required repair work immediately, making sure that machinery operates within risk-free parameters.Regular assessments and upkeep by qualified specialists likewise alleviate the chances of unexpected failures, which can cause hazardous circumstances on the production floor. By making use of these services, companies promote a society of safety that prioritizes staff member well-being. In addition, compliant and updated tools sustains adherence to industry policies, reducing lawful risks related to workplace safety and security violations - Packaging Equipment Repair Services.Ultimately, investing in professional product packaging equipment repair work services not only safeguards workers yet likewise enhances operational performance, causing an extra effective office environment

Often Asked Concerns
Just how Do I Choose the Right Product Packaging Equipment Repair Service?
Choosing the best product packaging equipment repair work solution involves examining knowledge, client testimonials, action times, and service warranty alternatives. In addition, examining the service's familiarity with details tools and schedule of components can greatly influence the decision-making procedure.
What Types of Product Packaging Tools Can Be Repaired Skillfully?
Numerous kinds of product packaging devices can be repaired expertly, including filling up makers, labeling devices, securing makers, and palletizers. Each kind requires specialized knowledge to assure efficient fixings and maximum operational efficiency in product packaging procedures.
How Often Should I Arrange Upkeep for My Product Packaging Equipment?
Arranging maintenance for product packaging equipment need to happen every three to six months, depending upon usage strength and producer referrals. Normal maintenance assurances peak performance, prolongs equipment life-span, and decreases unforeseen failures that could interfere with operations.
Exist Service Warranties on Repair Works Provided by These Providers?

What Should I Do if My Tools Breaks Down Suddenly?
When devices breaks down suddenly, it is suggested to examine the problem, assurance safety and security, consult the manual for repairing pointers, and contact a certified technician for expert support to lessen downtime and visit this website guarantee reliable repair work. Correct upkeep with expert product packaging devices repair services considerably contributes to boosted equipment durability. Prompt repair services and normal assessments ensure that machinery operates within suitable specifications, lowering the danger of tragic failures.Moreover, specialist repair service services frequently use top quality substitute parts, which can significantly prolong the life-span of equipment. With skillfully repaired tools, staff members can concentrate on their core tasks rather than troubleshooting malfunctioning machines.The dependability of well-kept packaging equipment contributes to smoother operations, enabling companies to enhance their manufacturing procedures. Their experience covers numerous equipment types and brand names, enabling them to swiftly diagnose problems and apply efficient solutions.Moreover, professional repair work technicians stay updated on technologies and best techniques, making sure that fixings are executed effectively and efficiently. Well-kept devices greatly minimizes the threat of crashes, injuries, and equipment malfunctions.
Report this page